Energy Efficient Motors
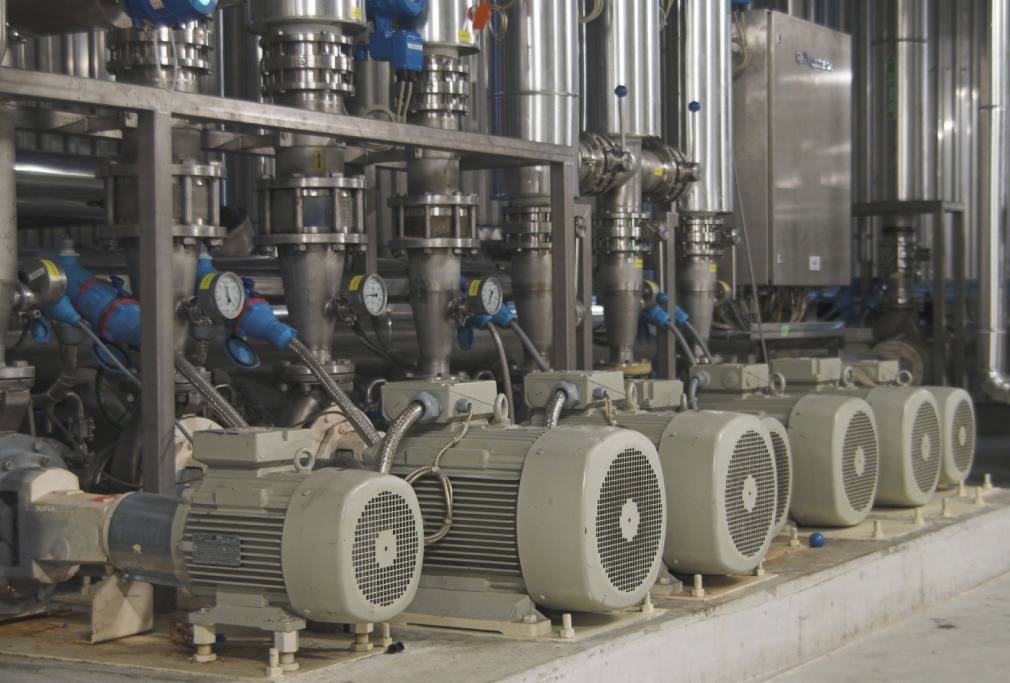
India’s industrial sector contributes around 25.92% of its GDP, making energy efficiency critical for sustainable growth. As the third-largest energy consumer globally, India’s energy demand is expected to double by 2040, according to the International Energy Agency (IEA). One of the government's primary strategies to meet this growing demand is transitioning to energy-efficient systems, particularly electric motors, which account for over 50% of electricity consumption in industries. Electric motors are widely used in various applications, including induction motors, pumps, and fractional horsepower (FHP) pumps, where energy efficiency is crucial.
Among various sectors, the adoption of energy-efficient motors in fans is gaining importance. Ceiling fans are widely used in Indian households and industries, and upgrading their motors can significantly reduce energy consumption. Transitioning from IE2 to IE3 motors, which are classified as high-efficiency motors, is crucial. IE3 motors consume less electricity while providing the same output, contributing to substantial savings on energy costs and reducing carbon emissions.
Copper's Role in Energy-Efficient Motors
Copper is essential in manufacturing electric motors due to its superior conductivity, durability, and malleability. In ceiling fans, the copper used in motor windings significantly enhances the motor’s efficiency. With copper’s higher conductivity, motors experience reduced energy losses and generate less heat, making them more energy-efficient. This allows for smaller, lighter motors without compromising performance.
In induction motors, copper's excellent conductivity plays a vital role in improving efficiency and performance. Copper windings in these motors help reduce electrical resistance, which in turn minimises energy losses. This characteristic makes copper motors highly efficient for various industrial applications, ensuring they operate optimally even under heavy loads.
For pumps and FHP pumps, the benefits of copper motors are equally notable. These motors, which often operate continuously, require materials that can withstand high operational demands. Copper's durability and heat dissipation capabilities ensure that these pumps run efficiently, lowering energy consumption and extending the lifespan of the equipment. The use of copper in motor design enables manufacturers to create pumps that deliver reliable performance while minimising energy usage.
Moreover, advancements in copper die-cast rotor technology have revolutionised motor manufacturing. Replacing traditional aluminium rotors with copper can increase a motor's efficiency by up to 5%, reducing heat loss and extending the motor’s lifespan. The benefits include lower energy costs, reduced temperature rise, and improved overall performance, making copper motors ideal for energy-efficient fans, induction motors, and pumps.
National Motor Replacement Program
The Indian government, along with organisations like the International Copper Association India (ICA India), has launched initiatives like the National Motor Replacement Program (NMRP) to create awareness about the adoption of IE3 motors. This program provides industrial stakeholders access to energy-efficient motors at affordable costs, accelerating the transition to sustainable practices.
What We Do
ICA India works towards raising awareness about energy-efficient motor systems in various applications, including ceiling fans, induction motors, and pumps. Through partnerships with key stakeholders, ICA India creates awareness about the use of copper in motors, advocates for favourable policies, and supports the adoption of advanced motor technologies. With copper’s unparalleled properties, energy-efficient motors in these applications are paving the way for a more sustainable future.
Resources
No posts found!